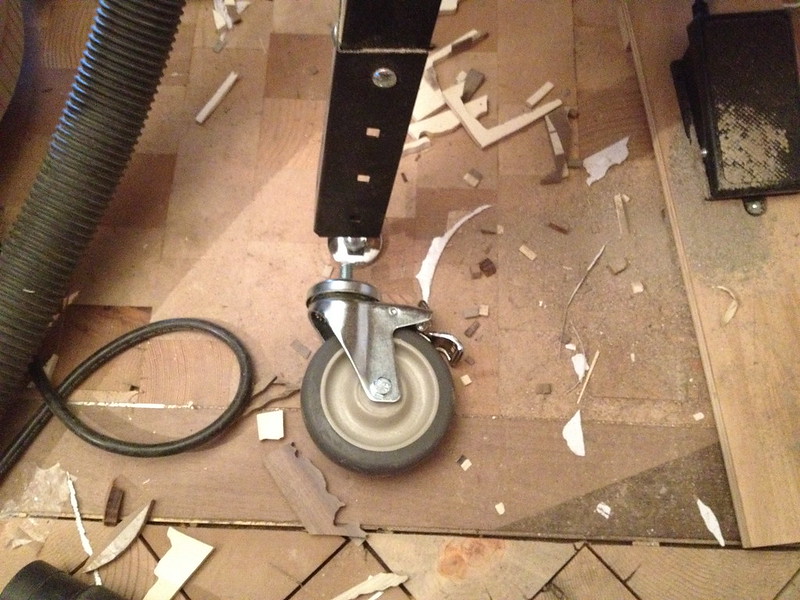
Industrial caster wheels are best constructed from stainless steel. These casters are exposed to harsh chemicals, water, and extreme temperature fluctuations in manufacturing facilities that would quickly corrode less durable casters.
Stainless steel casters can help you improve your workplace infrastructure by creating more fluid movement throughout the facility. This frees up building space and makes your workspace more accessible for everyone.
Durability
The durability of stainless steel castings, like Hamilton casters, makes them ideal for manufacturing parts under continuous stress. They can also withstand extreme temperatures, abrasion, and corrosion without any damage. This makes them an excellent choice for pump and valve components and piping systems.
The process of stainless steel investment casting involves creating a pattern made from wax and then dipping the wax model into a substance, which can be ceramic slurry or white industrial latex. Once the wax is dipped, it is covered with sand stucco to make a plaster mold.
Stainless steel castings are often machinable after production, which can help to reduce costly machining costs. They can also be subjected to surface treatments, such as passivation and electro-polishing, for improved corrosive resistance. These processes can also provide a mirror finish to improve aesthetics. This is particularly important for medical applications requiring sanitary stainless steel parts. Examples of these include catheters, surgical tools, and X-ray equipment.
Corrosion Resistance
The chromium in stainless steel investment castings creates an oxide layer on its surface that resists corrosion. If the oxide layer is damaged, it will build up again. This feature makes stainless steel more resistant to corrosive liquid environments and oxidation than other metals.
The alloy elements in stainless steel also help it fight heat and corrosion. Nickel and molybdenum improve its mechanical prosperity, while chromium makes it more resistant to chemical corrosion. This makes it a good choice for industrial applications, including water and gas treatment systems.
Stainless steel is ideal for valve components and pump parts because it prevents leaks and promotes efficient fluid flow. It is also widely used in food and beverage processing equipment due to its hygienic properties.
Hygiene
Stainless steel castings can be easily cleaned, making them ideal for use in food processing equipment or other sensitive environments. They can also be sterilized without losing their durability and other properties. They are safer than aluminum, which can rust in certain conditions, such as high-salt or chlorine-containing environments.
Chromium and oxygen undergo a chemical reaction that results in chromium oxide, an invisible coating that shields the metal from corrosion. This protective layer is known as the “oxide skin.” When this surface becomes damaged, a new layer quickly builds up. This protects the material from rust, oxidation, and corrosion.
Investment casting of stainless steel entails creating a mold for the finished item. Once the wax model is completed, a tree assembly is inserted into it, and then the mold is dipped into a ceramic slurry. This is repeated until the shell achieves an adequate thickness. The shell is then dewaxed, and molten stainless steel is poured into it to produce the final cast component.
Versatility
Stainless steel castings can be created in various sizes and shapes to match the buyer’s specifications. Unlike welding, which can only create a single piece of metal at a time, casting can produce multiple casts quickly. This helps to increase the efficiency of production and cuts costs.
The process of stainless steel casting begins with creating a wax or ceramic pattern.
The liquid metal is then cooled to room temperature, removing the refractory. This leaves the stainless steel casting, which can be mechanically processed, heat treated, and inspected before being shipped to the customer. This versatility helps improve manufacturing efficiency and reduces cost while maintaining quality.
More Stories
How Barrel Air Cleaners Improve Engine Performance: A Comprehensive Guide
Guarding Your Haven: The Essential Role of Regular Roof Inspections in Home Maintenance
Key to Success: How Online Piano Classes Can Transform Your Skills